Un gain de temps et d’économie considérable
Une pièce en acier de 12 pieds, produite par impression 3D, a permis à l’Armée des ingénieurs des États-Unis d’économiser plus d’un an de délai de fabrication et d’éviter une fermeture de voie navigable de six mois, qui aurait réduit le PIB américain de 1,1 trillion de dollars et menacé 11 millions d’emplois.
L’importance critique des écluses de Soo
Situées à Sault Ste. Marie, Michigan, les écluses de Soo, construites initialement en 1855, sont cruciales pour le transport maritime, en particulier pour l’acheminement du minerai de fer, du charbon, des grains et d’autres commodités à travers les États-Unis. Ces écluses sont exploitées par le Corps des ingénieurs de l’armée des États-Unis (USACE) et figurent parmi les écluses les plus fréquentées du monde en termes de tonnage de marchandises manipulé.
Une innovation majeure dans l’infrastructure civile
En mars, les ingénieurs de l’armée ont installé le plus grand composant jamais produit par une imprimante 3D dans l’infrastructure civile américaine. Il s’agit d’une partie métallique de 12 pieds de long pour le système d’arrêt des navires sur l’écluse Poe, l’une des deux écluses actives des installations des écluses de Soo.
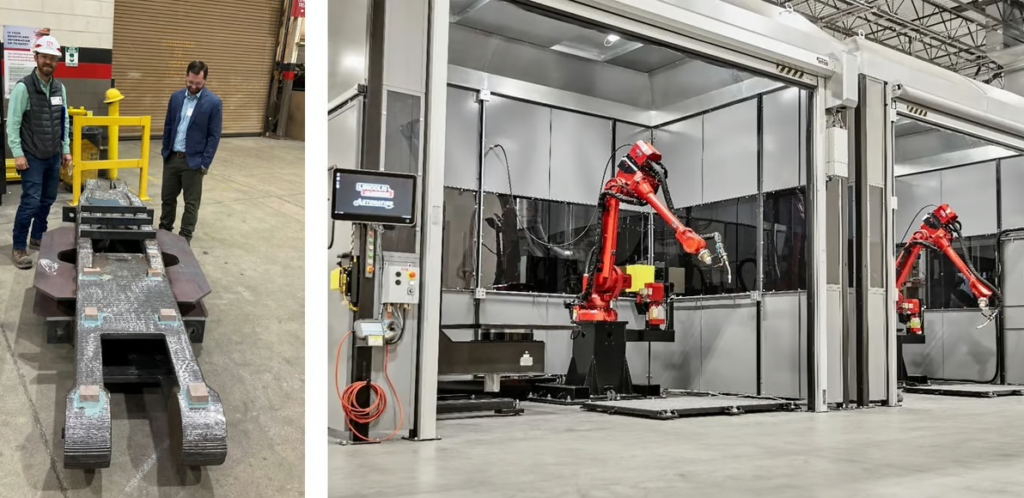
Une collaboration fructueuse
Après la découverte de fissures dans l’un des bras de 60 ans en février 2023, les ingénieurs ont sélectionné la fabrication additive, en particulier la fabrication additive par arc avec fil (WAAM), comme la meilleure option pour un remplacement permanent. Le contrat d’impression 3D a été attribué à Lincoln Electric, en collaboration avec l’USACE, pour produire la pièce en deux segments, ensuite soudés ensemble à Detroit.
Avancées et implications futures
L’Armée américaine et le Département de la Défense ont étudié en profondeur comment la fabrication additive pourrait être utilisée dans les projets militaires et appliquent désormais les leçons apprises pour moderniser l’infrastructure américaine. Un accent particulier a été mis sur la fiabilité, l’utilité et l’efficacité des coûts de la fabrication additive, en tenant compte des contraintes sévères imposées à l’infrastructure civile.
Une performance mécanique validée
Des recherches approfondies ont été menées pour caractériser les propriétés matérielles des pièces d’origine et garantir que le matériau imprimé en 3D puisse répondre ou surpasser leur performance. Les résultats ont montré que la pièce imprimée en 3D était au moins 20% à 30% plus solide que les métaux précédemment utilisés.
Un inventaire de pièces numériques
Les efforts de l’ERDC vont également créer un inventaire numérique de pièces, accélérant ainsi le délai de fabrication des composants de remplacement et éliminant le besoin de stocker physiquement de grandes pièces et moules pour une utilisation future. Cette initiative pourrait réduire considérablement les délais d’approvisionnement pour une large gamme de projets d’infrastructure.
Le succès du projet de l’écluse Poe
La pièce a été fabriquée en 12 semaines, contre un délai de 18 mois pour une fabrication conventionnelle. Elle a été installée, testée et mise en service lors du cycle de maintenance hivernale des écluses de Soo, réouvrant pour la saison de navigation le 22 mars. Cette réussite marque un tournant dans l’utilisation de l’impression 3D métallique pour l’entretien et l’amélioration des infrastructures critiques américaines.
GIPHY App Key not set. Please check settings